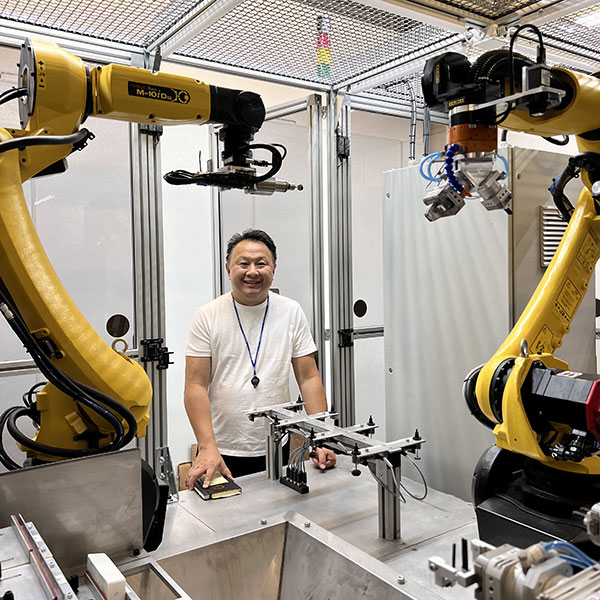
To veterans of the jewelry industry, the name Christian Tse likely calls to mind high-end platinum jewelry in a distinctive mesh style. The L.A.-based designer founded his eponymous designer jewelry line in 1996 and quickly garnered a reputation for innovation, winning awards and attracting a steady stream of high-end retailers to his work.
In 2003, a customer of Tse’s approached him about manufacturing his signature platinum mesh for a private-label venture. The project was a success, and his private-label business took off. “Over the years I started understanding there was a bigger need for private-label manufacturing and there was more consistency when I worked with brands,” Tse tells JCK. “They’d order and pay on time. There were no returns.”
From the start, Tse employed technology that he borrowed from other industries and modified for use in jewelry (he’d often visit automotive and medical trade shows to see what was new). At first, he used electronic machines to solder chains before moving on to primitive CAD and 3D printing systems.
About six or seven years ago, Tse, whose company is based in a 6,500-square-foot factory in Monrovia, Calif., took a leap into the future of fine jewelry manufacturing when he transitioned from wax 3D printing—a process followed in most cases by traditional casting—to 3D printing directly in gold and platinum.
In 2019, Tse founded an additive manufacturing company called Formula 3D that develops ionized gold, platinum, and silver powders, partnering with a printer-maker in Massachusetts called Desktop Metal to execute the designs. “We are like the ink manufacturer and they are the printers,” Tse says.
Now, Tse is convinced that cutting-edge technology, some of which he’s using to make jewelry for today’s leading luxury brands, will soon help more jewelers fill the gap created by the lack of talented craftspeople.
“The whole industry has a challenge of finding talent in terms of jewelers and setters,” Tse says. “I was trying to be creative: How does one grow and expand their business at a time when our business is thriving, but we can’t find enough support to manufacture?”
Taking a page from companies like Tesla, Tse embraced robotics about a year ago, when he introduced a custom version of the VDK-2300 jewelry processing system developed by Flexible Robotic Environment, a Serbian company that specializes in robotic technology for the jewelry industry. The system can polish most rigid jewelry designs such as rings, earrings, hard bracelets, pendants, and brooches.
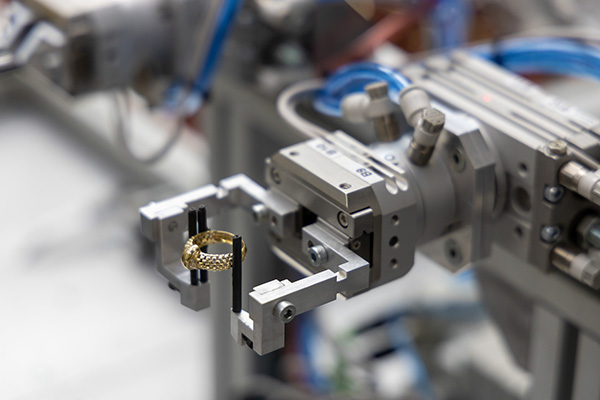
“They are two-arm robots, straight from the automotive industry, where they’re using robots to polish and spray-paint cars,” Tse says. “And we have another machine that sorts diamonds. We can pour thousands of diamonds in a bin and the machine sorts them into little trays, taking an information profile—the size and diameter, the crown angle, all of that is recorded in a database.”
The trays of diamonds are then passed on to another robot that can set the stones with an unprecedented degree of precision. “When you see the robot working and it’s actually picking up and setting melee that’s 0.6 mm, your mind can’t fathom how machines can do this so accurately.”
The accuracy and efficiency enabled by technology are helping Tse cope with soaring demand for his services. Indeed, demand is such that he is currently renovating a 20,000-square-foot facility in Monrovia that’s due to be ready by the end of this year.
“We are over capacity now,” he says. “Existing clients are asking us for more. This is where our robotic polishing machine and setting is coming into play.”
On the horizon is an even more powerful technology enabled by artificial intelligence. Tse is currently creating AI-assisted design software, through a company called Bling, based on an AI platform developed by Nvidia.
“We’ll draw a line on an iPad and it will turn instantly into a band ring,” he says. “You let the computer know if you want diamonds there or rubies. It will do that instantly with prongs that are correct and connected to the ring.”
In about two years, Tse hopes to partner with retail jewelers, who can offer the AI-assisted design software to customers interested in customizing their jewelry online.
“Once a user designs their own ring, the computer will send the digital files and our machines will start manufacturing those pieces,” he says. “The goal for that team is that once we receive the designs and it hits our machines, we can ship in 24 hours. Someone can design on a Thursday and by Saturday you’ll have your ring.
“We have CAD designers in-house and it takes three days to a week to finish one CAD design,” Tse adds. “And with this, someone who has zero knowledge of jewelry can design their own ring in minutes. I think it’ll give more power to consumers to customize what they want. And it’s less than a couple years away.”
Top: Christian Tse in his manufacturing facility in Monrovia, Calif., where he uses robots for polishing and gem-setting (photos courtesy of Christian Tse Design & Manufacturing)
- Subscribe to the JCK News Daily
- Subscribe to the JCK Special Report
- Follow JCK on Instagram: @jckmagazine
- Follow JCK on X: @jckmagazine
- Follow JCK on Facebook: @jckmagazine