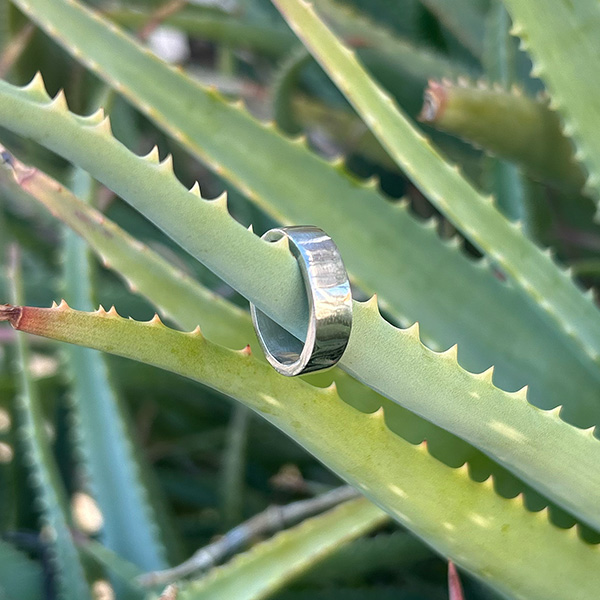
Earlier this month I was among a group of 10 trade press editors who converged on Miami to join Platinum Guild International (PGI) for a refresher course on the white metal centered on a daylong jewelry-making workshop at the Miami Jewelry School.
I came into the experience with what I thought was a fair bit of knowledge about platinum: naturally white precious metal, rarer than gold, hard to work at the bench, relatively heavy, luxurious.
At our welcome dinner, however, a Jeopardy!-style ice-breaker quiz underscored how tenuous my knowledge of platinum really was. (In 1590, prospectors panning for gold in South America discovered it, naming it platina, or “little silver.” Who knew?)
Platinum’s key qualities
The next morning, during the information session that preceded our jewelry-making experience, PGI senior vice president Kevin Reilly reminded us about platinum’s key characteristics:
The metal is pure to the tune of 90-95%, compared with 58.5% purity for 14k white gold.
Platinum is rare—30 times rarer than gold, to be exact. “All the gold ever mined could fit into three Olympic-sized swimming pools, while all the platinum ever mined would fill one pool up to your ankles,” Reilly said.
Platinum is 60% heavier than 14k gold, and 40% heavier than 18k gold. “A six-inch cube of platinum weighs 165 pounds,” Reilly said, offering a detail that goes a long way toward explaining why platinum feels so significant.
But until I actually sat down to work the metal with my own hands, I couldn’t connect all these characteristics into a single cohesive argument for why couples searching for wedding rings in a white metal should always opt for platinum.
At the bench
At first I was a little apprehensive. I had never sat at a jewelry bench. That’s because I’m not very dexterous; making things with my hands is not a strong suit.
But Marc Thurn, owner of the Miami Jewelry School—a platinum lover with jewelry in his blood (born and raised in Germany, he is the nephew of world-class gem cutter Bernd Munsteiner)—helped allay my fears.
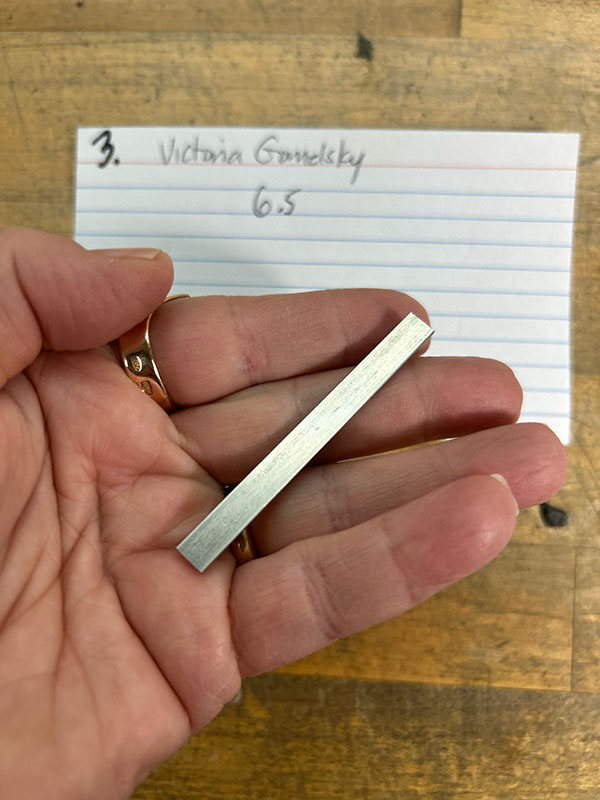
Over the course of about four hours, he and his team of instructors helped me transform a flattened bar of platinum into a shiny round band that I am proud to wear on my ring finger (stacked with my custom spinel ring for a perfect two-tone pairing).
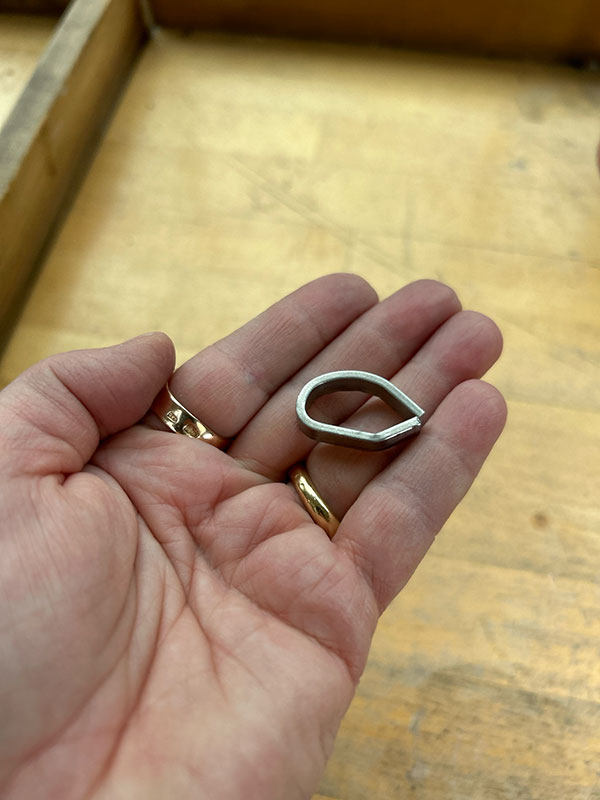
The first step—bending the metal into a round shape that approximated the general silhouette of a ring—was the hardest in terms of the physical exertion it required.
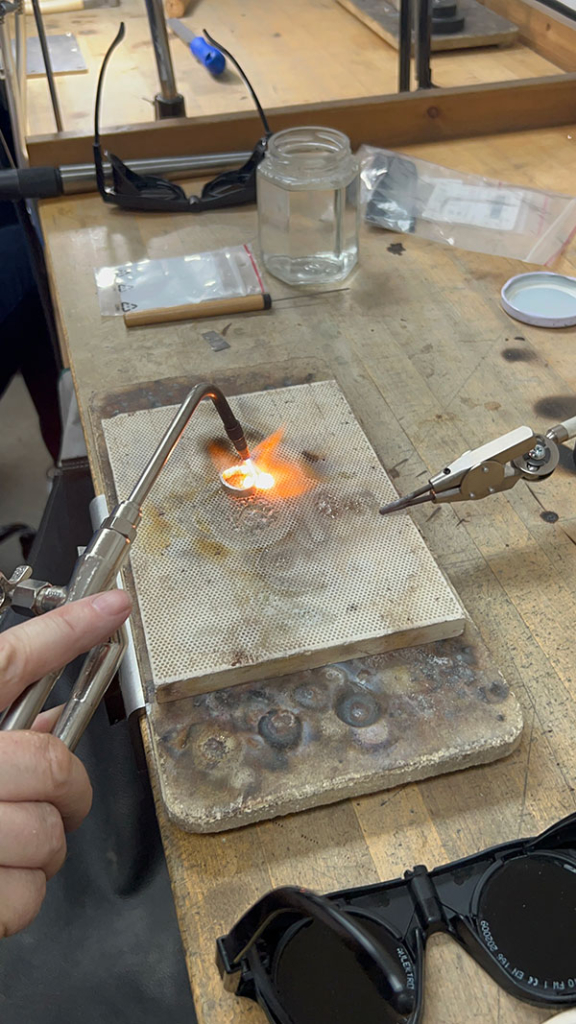
The next steps—hammering, annealing, hammering some more, and soldering—were more time-consuming than I anticipated. I definitely needed help in manipulating the metal. As I placed my not-quite-ring on the tapered tool known as a mandrel (or triblet?) and brought a hammer down on it to shape the ring into a round shape, I worried for my fingers. Was I at risk of injury? Probably.
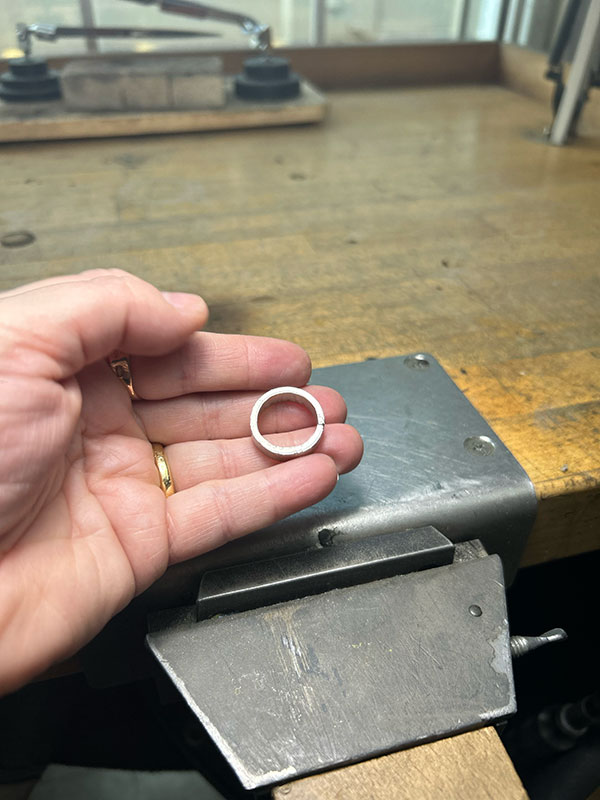
As we moved on to filing and sandpapering our rings to remove the tool marks and dings, I was reminded of another key characteristic of the metal: Unlike white gold, which loses a bit of metal with every scratch, platinum endures.
Here’s how PGI puts it: “When platinum is scratched, metal is displaced, rather than flaked and lost, as with other metals. Over time, the surface of a platinum ring will reflect a satiny finish, often referred to as a patina. It’s platinum’s mark of authenticity and evidence of its superior wear resistance, making it supremely wearable and the ideal metal for heirloom-quality jewelry.”
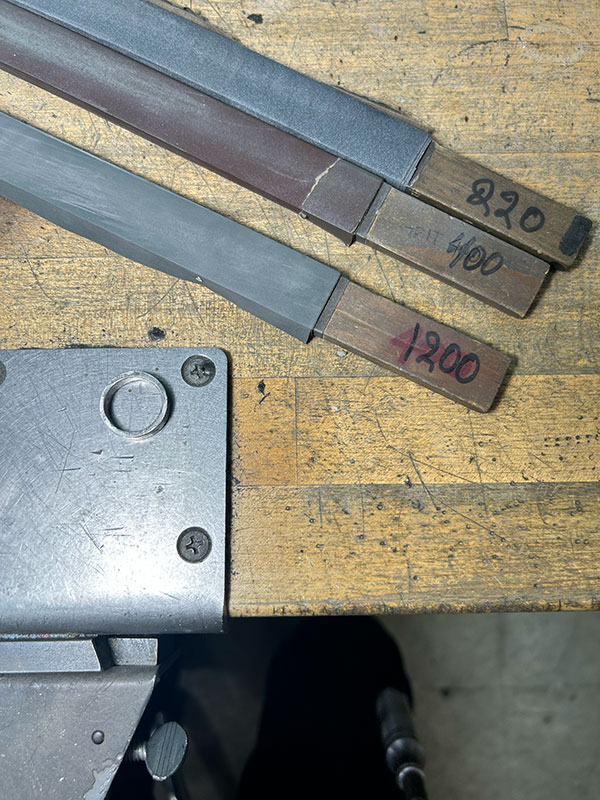
Reilly offered an analogy that helped me visualize what happens when a platinum ring gets knocked: Imagine pressing your finger on a stick of butter. The material is displaced, but the butter fundamentally remains.
Next came the filing process, which struck me as incredibly nuanced. My untrained eyes couldn’t figure out when the tedious work of sandpapering was sufficient. (I kept insisting I was going for a “rustic look” in order to justify calling it quits.)
My takeaways
Finally, after seeking help from the instructors yet again, my ring was ready for the final stages: polishing and cleaning. What emerged from the final dunk in the ultrasonic cleaner was a shiny wide band that looked, at least upon first glance, like something I might find in a retail showcase.
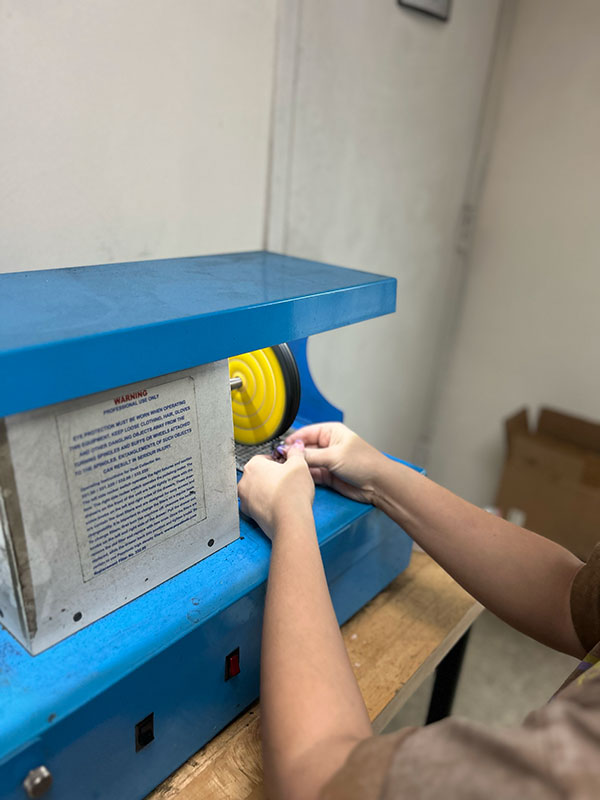
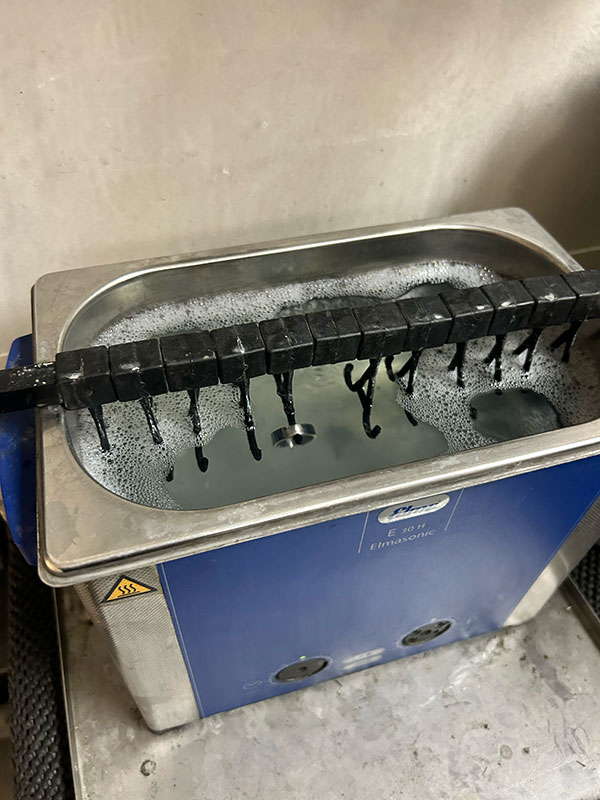
It would not fade to any other color over time, nor require replating. For all intents and purposes, I had made something truly eternal.
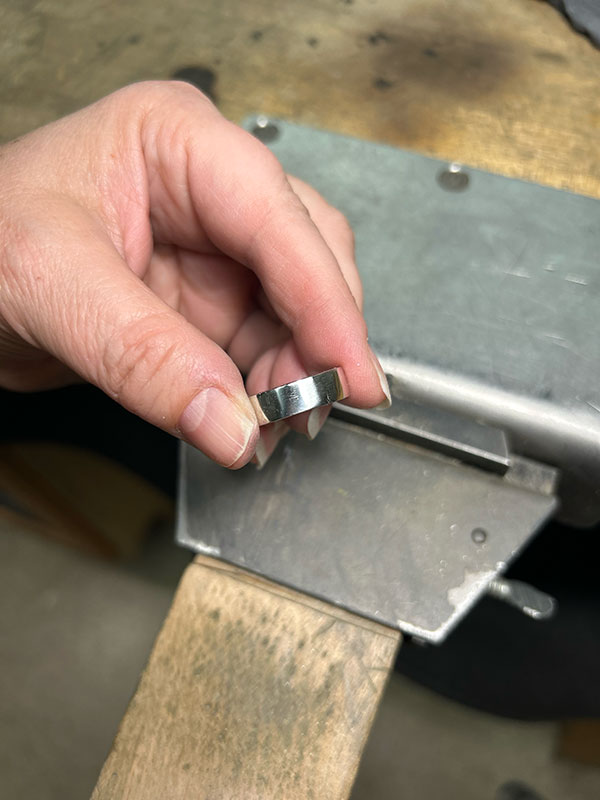
As I admired my handiwork, I thought back to something else we learned during the workshop: that retailers and bench jewelers, not consumers, are the real stumbling blocks preventing the metal from achieving more widespread acceptance, particularly for wedding rings.
What a missed opportunity. For a metal that has an intrinsic sense of luxury, with a raft of the very characteristics you would use to describe a successful marriage (rare and enduring, with a beautiful patina that develops over time), platinum checks all the physical and emotional boxes.
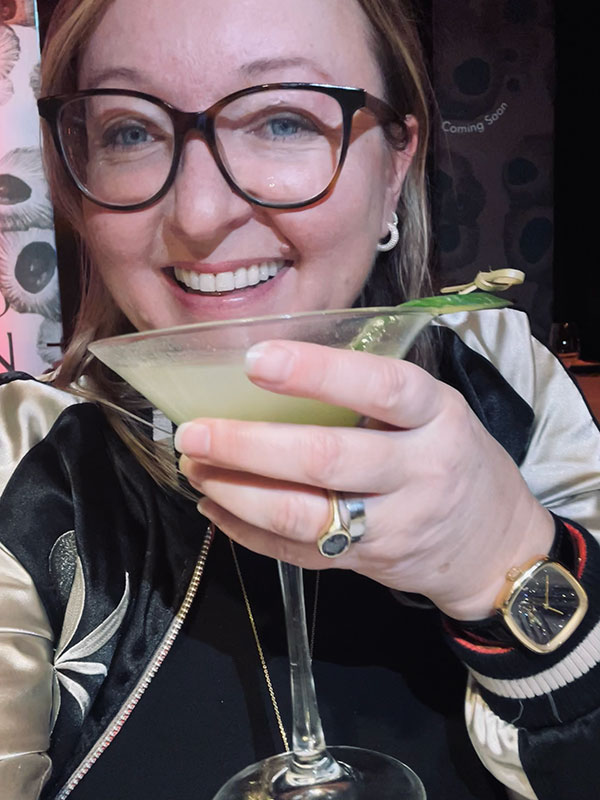
Sure, there’s a learning curve involved in working with the metal. It lacks gold’s familiar malleability. But let me tell you, when you’ve made your way through the platinum jewelry-making crucible, as I have, you’ll appreciate it all the more.
Top: My new platinum band hanging out in my backyard
- Subscribe to the JCK News Daily
- Subscribe to the JCK Special Report
- Follow JCK on Instagram: @jckmagazine
- Follow JCK on X: @jckmagazine
- Follow JCK on Facebook: @jckmagazine