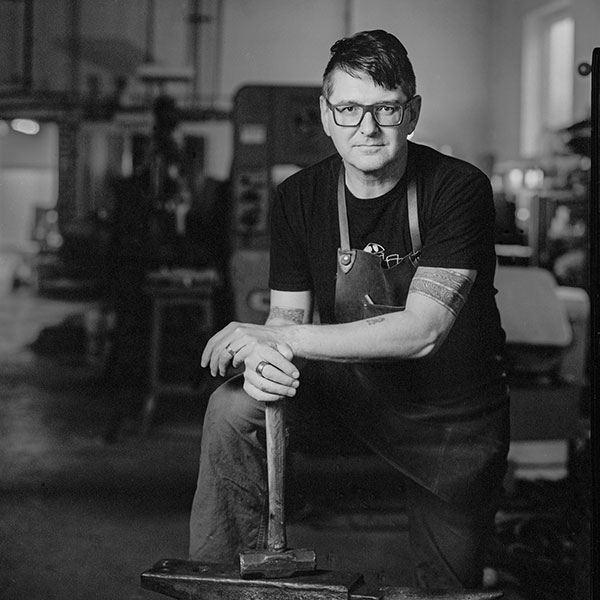
Whether it started with a museum blacksmith, his grandfather’s millwork, or his own expertise with bicycles, Chris Ploof is fascinated with how people use their hands to create useful, well-crafted things to get them from one thing to another.
That early interest in science, engineering, and craftsmanship would prove instrumental at every stage of Ploof’s life, whether it was during his time in the U.S. Army, working in the bicycle industry, or partaking in his hobby as a Civil War reenactor. Now, with his efforts in the jewelry industry, that fascination with how metal moves and transforms has reached an apex in Chris Ploof Designs, he says.
If there’s a through line for all of these interests, Ploof says it is his love of taking things apart, finding a way to put them back together, and making something amazing as a result.
“I think the mechanical aspect of working on bicycles translates to the mechanical aspect of making jewelry as well as the maintenance of the tools and machines we use to make our jewelry,” Ploof says.
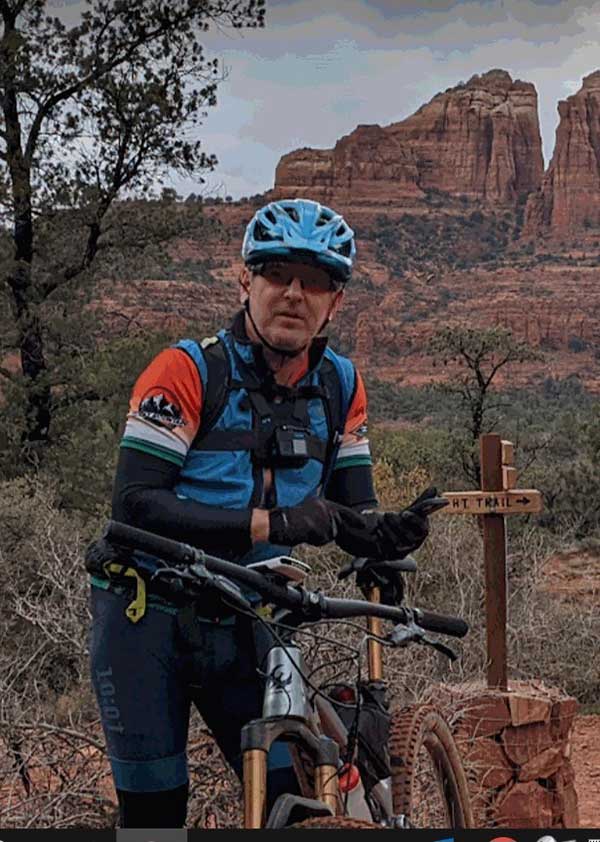
Ploof also looks to the past and the future for his inspirations.
“History definitely informs our techniques,” Ploof says. “I like to think we practice historical techniques with Damascus steel and Mokume gane with a huge dose of modern engineering applied. Our techniques help guide some of our designs, and I am always looking to history for jewelry inspiration.”
Ploof says Mokume gane is an ancient Japanese metalworking technique that he and other modern-day jewelers now use. The result is a layered design that resembles natural wood grain.
As far as looking toward the future, that includes how he chooses to work. His Chris Ploof Designs studio is solar powered, which speaks to his desire to be sustainable in his tools, techniques, and material choices.
“We’ve always ethically sourced materials and gemstones, and we are now proud to say we are producing 135% of our energy needs with a new, 37,000-watt array of solar panels,” Ploof says. “This is enough to power our shop, our home, and allow for electric-vehicle charging.”
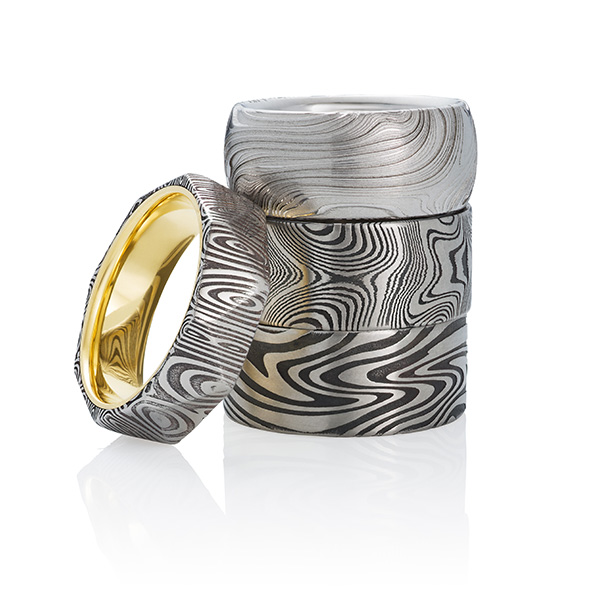
Ploof’s story starts in Massachusetts, where he first saw big machines in his grandfather’s work as a superintendent at a huge mill complex. Watching the tinsmith and blacksmith while visiting a local living history museum also grabbed his attention.
“It was the ability of the blacksmith to take metal—this unyielding, hard, strong material—and to fashion it into useful and necessary tools,” Ploof says. “All other skills benefit from the blacksmith’s ability to manipulate metals into tools that help you complete a job.”
His first job came as a salad and dessert prep chef at a local diner, which taught him about punctuality and teamwork. Those lessons proved necessary as he got more into cycling, which he loved to do with friends, and taking long rides in between his deployments in the Army.
That is also when he started to do Civil War reenactments, where his love of blacksmithing turned into a talent for crafting everything from tent stakes to irons to cooking gear.
That military background also fed his understanding of how to work well with others as well as general attitude—“Never give up,” Ploof says—and how to make a plan.
His full-time career was in the cycling industry, doing everything from serving as a sales manager to service manager to team mechanic. Eventually, he was the head mechanic and trainer of a multi-store bicycle retail chain.
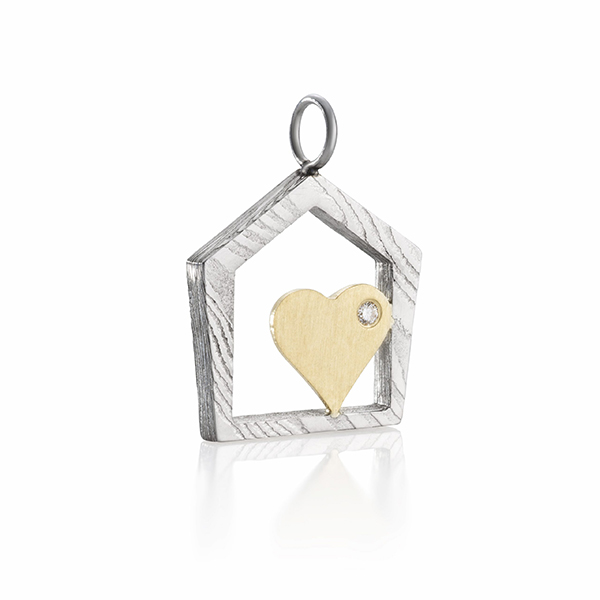
Around this same time, Ploof says he took an interest in learning how to cast bicycle parts of his own design. The only classes he could find were focused on jewelry, but he figured that work would translate. Instead, he found jewelry as intriguing as anything else he had encountered in his lifelong desire to know how things are made.
“I work a lot in bridal, crafting one-of-a-kind wedding bands with unique materials,” Ploof says. “The whole process of getting married and choosing a ring is as thrilling as riding a bike down a mountainside. Every ride is a different experience, and that is why I love it.
“Similarly, each and every ring that we handcraft has its own unique design,” Ploof says. “I like to say that we practice the art of the fingerprint or the art of the snowflake. But unlike the ephemeral nature of an experience like an awesome bike ride, the heirloom-quality jewels I now create will stand the test of time and endure for generations.”
Top: Chris Ploof has lived an artist’s life, and his jewelry reflects that as he works in styles and materials such as Mokume gane, Damascus steel, and meteorite (photos courtesy of Chris Ploof).
Follow me on Instagram and Twitter
Follow JCK on Instagram: @jckmagazineFollow JCK on Twitter: @jckmagazine
Follow JCK on Facebook: @jckmagazine